The costs associated with carbon fiber make it among some of the more expensive materials and additives used, typically for use in auto mobiles, aeronautics and defense. That said, we are now beginning to see carbon fiber being incorporated into high density materials thanks to the development of new and improved compounding techniques for heavy plastics which are utilizing carbon fiber as an impact modifier or in order to produce conductive materials.
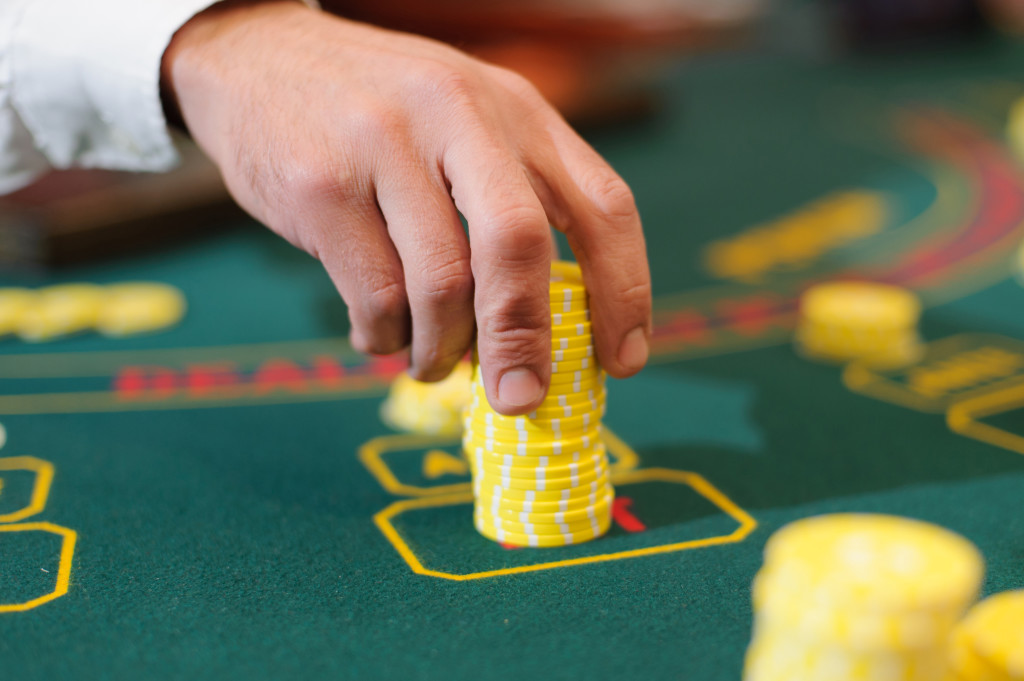
Companies are toggling with variable and economical solutions where pre-processed carbon fiber taken from unused fibers and cuts are repurposed as carbon fiber loaded pellets which can be used by standard injection moulding machines. These pellets are fed into molding machines and molded into hollowed out parts to offer further weight savings and less overall material usage. As a result, the #engineered thermoplastic tends to be 25% stiffer and 10% lighter than components that are made using 30% glass fiber reinforced PA6.
The biggest advantage offered by these pellets is that they’re among the best ‘low cost alternatives’ for those wanting to use carbon fibers without having to deal with countless economical and light-weighting challenges that such fibers may attract.
In fact, such a material was used to create clutch pedals and it turned out to be the perfect way to replace metal parts. The automobile industry has been constantly trying to shift to lightweight materials, and while these clutch pedals alone won’t get to the MPG target by themselves, it certainly moves the needle. On the opposite end of the material spectrum, when weight is the goal and not the problem, carbon fibers are also being used in high gravity compounds used in weighting applications as a way to expand the spectrum of available physical properties for these heavy plastics.
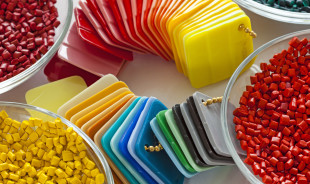
Sure, these high density materials won’t compete with carbon fiber structures because of the necessary impact performance, but they can be used easily in places that use injection moldable parts and offer an increase in stiffness and impact strength right away.
And while these heavy plastics might be more expensive in a like-for-like comparison, it’s not just about the cost per gram. One also needs to understand that since this is a stiffer material, it becomes possible to use less materials and thinner wall sections, thereby reducing overall production costs and cycle times!
0 comments:
Post a Comment