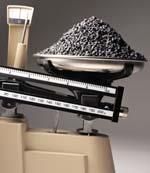
Health, environment and safety issues have been driving the demand for lead replacements, but it isn’t as easy as it looks like. Selecting and working with high-density plastics requires special care. Different types of materials suit different application purposes. The choice of high-density filler additive, as well as the selection of polymer matrix, has a huge impact on the properties of the material. There are other factors such as molding methods, barrel temperature, tool designs, processing speeds and parts handling to take care of as well.
Add More Weight without Disrupting Part Geometry
High-gravity compounds have a specific gravity that ranges between 2 to 11, unlike normal plastics which have a specific gravity of 1.0. To put things into perspective, even 40% long-glass reinforced nylon has specific gravity of 1.74. As a result, heavy plastics go a long way in increasing part mass as well as boosting perceptions of higher quality while allowing you to avoid traditional metal drawbacks such as higher costs, complex processing methods and design restrictions.
Getting Rid of Lead
The dangers posed by lead cannot be reiterated enough. Lead has been causing all kinds of health and environmental issues for a very long time, and the recent Flint fiasco was proof of just how dangerous the metal really is. Governments are now beginning to root out the use of lead, and this is where high-gravity compounds can really help you. They can replace lead in applications such as radiation shielding in the fields of x-ray equipment and nuclear medicine.
How to Choose the Right Materials
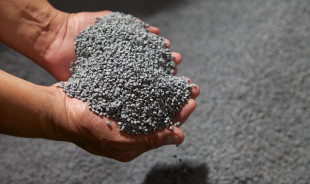
The first thing that you need to do is determine your application requirements such as electrical and mechanical performance and aesthetic as well as determining industry standards and regulatory requirements. There are all kinds of heavy plastics available and you can always mix different resin matrixes with high-density additives such as metal powders and minerals.
Mold Designing
Different high-density plastics have different properties and this has a major impact on mold design. One can always use traditional practices such as two-plate molds or three-plate molds and hot runner systems or cold runner systems, but some adjustments need to be made.
1. One of the first things to look at is the type of steel used. P20 works well for low volume operations, but as one increases volume and specific gravity, you need more abrasion-resistant materials.
2. A short flow length is needed to prevent the flow front from freezing under high-pressure situations.
3. Avoid the use of valve gates as high-gravity compounds don’t offer clean shut-offs.
4. Keep the flow front open for as long as you possibly can as this minimizes shear. Having a thicker wall makes this possible.
5. You need uniform pressure all over the part when it is pushed out of the cavity to prevent cracking.
How to Process Heavy Plastics
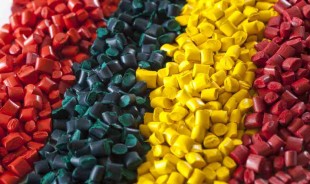
The simplest way to process high-density plastics is to use the injection molding method. Other methods commonly seen include sheet extrusion, profile extrusion and thermoforming. Here are a few things that you need to keep in mind while processing heavy plastics.
2. Reduce pressure in the die by using coarse screen packs and moderate screw rpm to
3. Avoid inconsistent fill by using moderate or fast injection speeds.
4. Offer uniform heating to control the mold temperature.
5. Hand loading might be necessary for materials that have a specific gravity over
0 comments:
Post a Comment