Thermoplastics refer to materials that have been made by polymers which have been linked with intermolecular interactions to form branched or linear structures. Think of the material as a set of strings that are mixed with each other on a table, and the greater the mixing, the more effort it needs to separate them from each other.
In today’s word, high density materials and thermoplastics have been quick to make a place of their own. They’re now dominating aviation and automobile markets as one of the greatest innovations in recent years, but are slowly making their way into all kinds of tools and appliances that are used in all spheres of life.
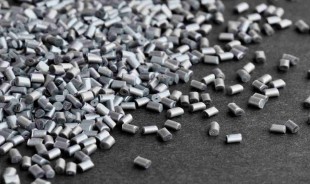
A revolutionary example of how thermoplastics have been successful in improving life was shown at a materials conference that is held in Europe each year. This conference presents many such revolutionary ideas that can completely transform the way we look at thermoplastics and high density materials. One such presentation was made by a team of researchers from Fraunhofer Institute for Chemical Technology (ICT) at K2016.
They narrated the progress shown in the Wind Blade Using Cost-Effective Advanced Composite Lightweight Design project, one that uses foam and high density materials to reduce the weight of rotor blades for wind turbines that are installed offshore as a means of increasing their service life. A miniature wind turbine made out of thermoplastics and foam was shown at the conference as proof of progress.
“We’re switching the material class and using thermoplastics in rotor blades for the first time,” says Florian Rapp, project coordinator at the institute. The main goal was to separate carbon fibers and glass in order to reuse the new high density material matrix as material for making other blades.
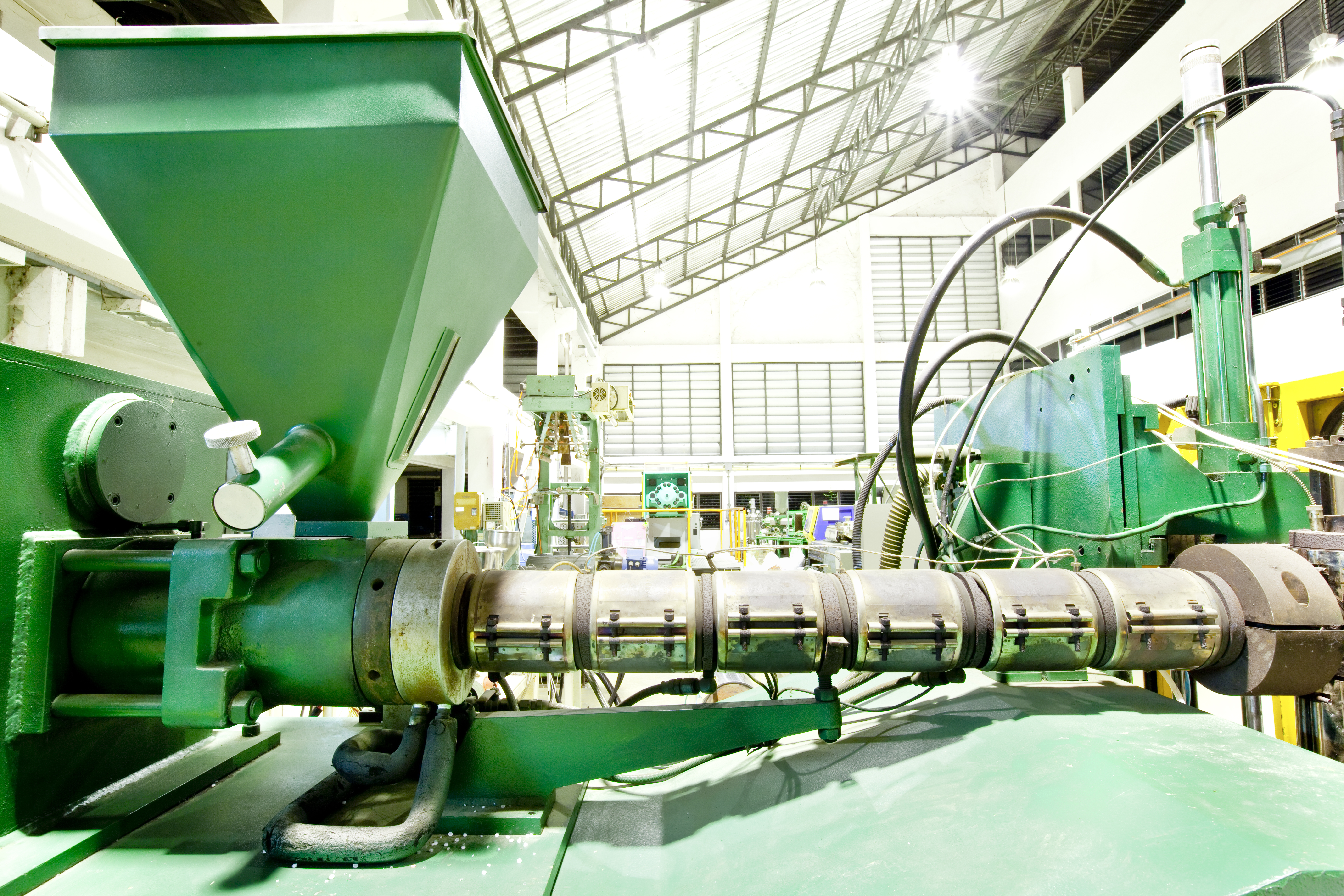
Researchers further state that carbon fiber reinforced thermoplastics are used for the areas that are made to bear the maximum weight, whereas glass fibers are used for the less stressed areas. The inner structure and the outer shell were made using FRP and thermoplastic foam. For the core, the team is developing thermoplastic foam that has been bonded with CFRT layers in a sandwich style design. This is expected to improve longevity, efficiency, durability and overall strength for the blade.
What makes thermoplastics and high density materials so important in all kinds of fields today is that they not only help to dramatically reduce weight, thereby maximizing efficiency, but are also known to be cost-effective and extremely durable solutions that can be used to save materials in all kinds of aviation and automotive applications. Says Rapp, “We’re breaking new ground with our thermoplastic foams,” and he really couldn’t have said it better!
0 comments:
Post a Comment