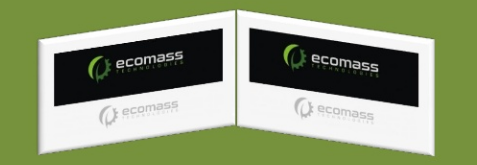
Bally Ribbon Mills (BRM), designer and producer of highly engineered woven fabrics, recently presented a specialized line for aerospace and aviation and aerospace. The fabrics satisfy detailed strength requirements for structural components. It’s woven webbing is already used at the International Space station and at NASA’s Mars Exploration Rover Opportunity, as well as in parachutes, cargo restraint systems, flight suits, flotation devices, air slides, seatbelts, and other safety systems.
BRM’s current groundbreaking fabrics contain a patented 2-D and 3-D thermoplastic composite materials and recently engineered E-Webbings. The Thermoplastic Composite Materials provide pinpointed reinforcement, specific superior strength, increased flexure, impact resistance, and resistance in varied molding/forming processes.
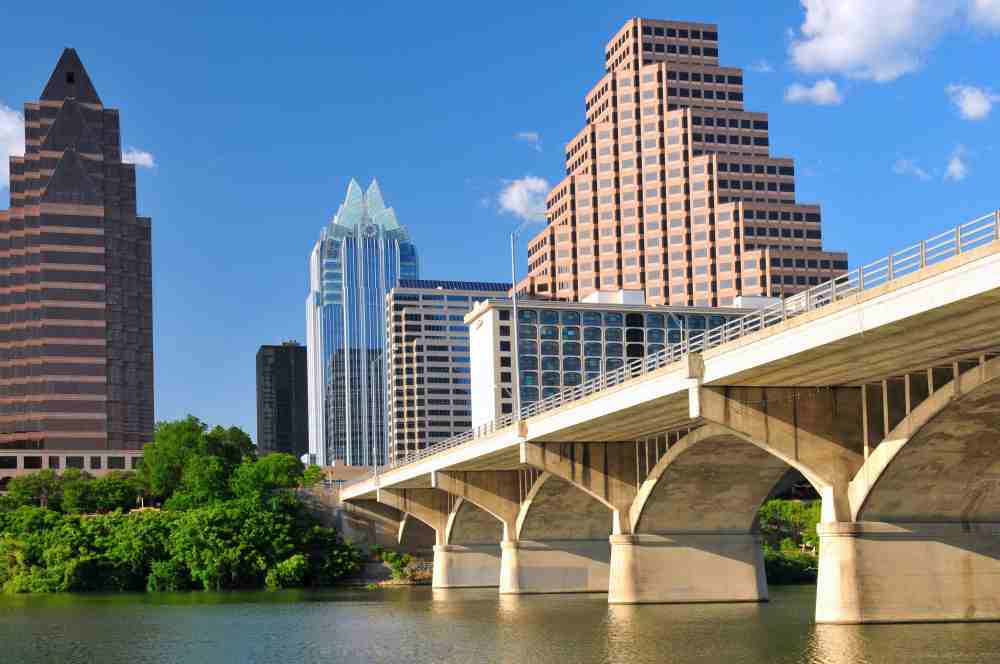
BRM designed the product line for the Internet of Things technology zone, which is intended for the individual, commercial, and military aircraft area. E-Webbings delivers conductive and structural components that integrate sensors and other equipment.
BRM designers and engineers apply a multi-dimensional, continuous weaving method to create lightweight, cost-effective, advanced woven 2-D and 3-D thermoset and thermoplastic polymer composite structures. Its products focus on durability and resist chemicals, abrasion, weather, and heat. As well as increasing safety, its lightweight webbing costs less than aluminum and steel and its unique production method can be customized to meet end user requirements.
Ecomass Technologies
Since 1998, Ecomass Technologies has produced innovative solutions through thermoplastic composite materials, high density polymers, and high density plastics. It specializes in high density and lead replacement applications, which can be utilized in a wide array of applications, including vibration dampening, radiation shielding, gamma ray shielding, and x-ray shielding.
Ecomass works with both government and commercial clients to solve issues, develop solutions, and meet application needs. Its never-ending training, skills, and experience in the formulation and development of high density thermoplastic compounds offers its customers the freedom to design and focus on form and function, while it solves the challenges their products face. Its goal is to enable its customers to design and produce the best parts possible by providing them with the highest-performance and lowest-cost materials so that they can succeed and prosper in their markets.
Ecomass’ high gravity compounds are designed to replace traditional high density materials such as lead and other metallic materials. Its high gravity compounds can be formulated up to the density of lead and deliver the weight and physical properties of metal with the design and production advantages of injection molded plastics. They can be injected or compression molded. Such eliminates the need for secondary operations and reduces costs.

Ecomass Compounds satisfy the international regulatory concerns of the international marketplace, are completely nontoxic, and meet the EU RoHS Directives
Ecomass’ customer service team is recognized for its skill and responsiveness. See its website for contact information and its RFQ Form. It’s probably already worked on the solution you’re seeking.
0 comments:
Post a Comment