Injection molding and the products thereof has
already infiltrated nearly every aspect of your everyday life. You’re
likely to see dozens of injection molded parts all around you, in your
car, at work, in your house, even in your wallet. Considered to be one
of the most versatile methods of production, injection molding is not
only simpler and more efficient than many other production technologies,
it is also more reliable.
INJECTION MOLDING ADVANTAGES
Use Different Types of Plastic Simultaneously
One of the biggest advantages of injection molding is the ability to be able to use various types of heavy plastics
for the same manufacturing process. Co-injection molding makes it
possible to combine high density plastics to get the desired properties
and reduce issues associated with specific plastics.

The cycle time usually varies between 15 and 30, making it possible to produce a large number of parts per hour.
Colour and Material Flexibility
Injection molding makes it possible to change the color of the engineered materials without causing too many problems.
Higher Efficiency
Injection
molds can be customized to meet exact pre-programed specifications to
make the actual manufacturing process faster. The high production output
and increased efficiency also makes the manufacturing process cost
effective.
Flexibility in Design
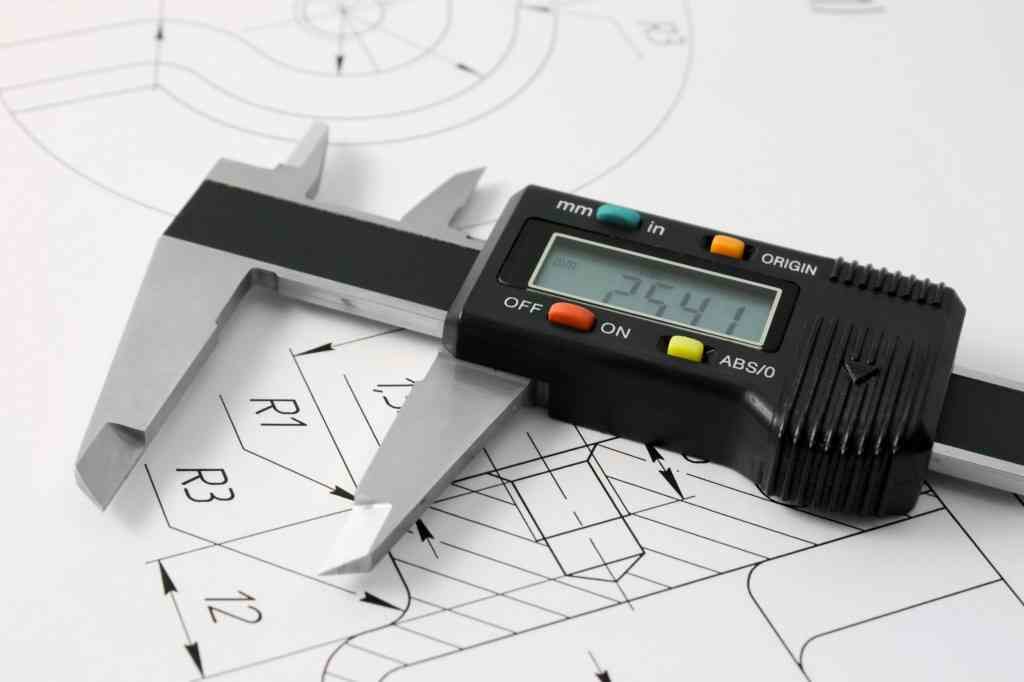
Parts
made using the injection molding process are extremely flexible. Since
the molds are subjected to high amounts of pressure, high density plastics
get pressed harder when compared to other molding processes. As a
result, it is possible to add all kinds of details in part design.
Moreover, due to the higher pressure, complex shapes can be easily
designed and manufactured.
Enhanced Strength
It
is possible to add fillers to your injection molds. These fillers
reduce plastic density while allowing for increased strength after
molding. Plastic injection is perfect for parts that need to be strong
as well as durable, and this an advantage that is unique to the
injection molding process.
Expensive Initial Tooling
Getting
a tool is a costly affair. And even if you plan to make it yourself,
you need to have the right skills and an injection molding machine, both
of which are expensive as well.
Difficult to Estimate Actual Costs
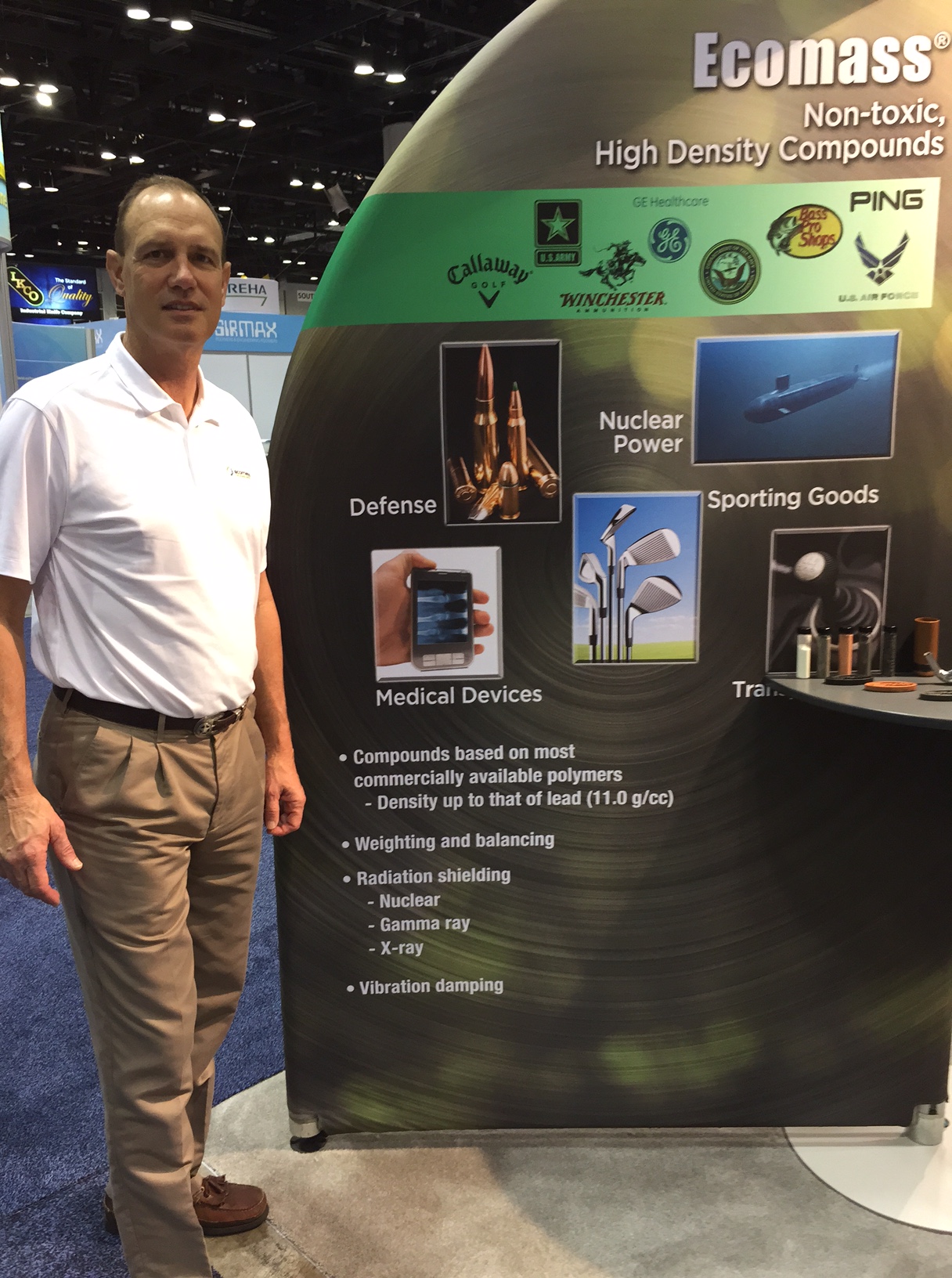
Injection
molding comes with a number of uncertainties and this has the tendency
to throw your budget for a toss. It always makes sense to account for
unforeseen expenses when using this manufacturing method.
Restrictions in Part Design
Despite
all its versatility, injection molding tends to place certain
restrictions on part design. The main thing to understand is that an
injection molding tool is made from two halves which need to be pulled
apart so that the part can be released from the tool. Therefore, you
need to make sure that your parts are perpendicular to the tool opening
and ensure that the maximum part thickness for any particular spot is
less than 2mm – 3mm.
THE BOTTOM LINE
Injection
molding helps to make your production process as easy and hassle-free
as possible. Most parts that are ejected from injection molding have a
finished appearance, and the scrap generated from this process is
environment-friendly and can also be re-used. Ecomass Compounds presents top-of-the-line high gravity compounds that are tailor-made to your requirements
and specifications to help you seamlessly replace metals or simply make
your manufacturing process easier and cheaper than before.
0 comments:
Post a Comment