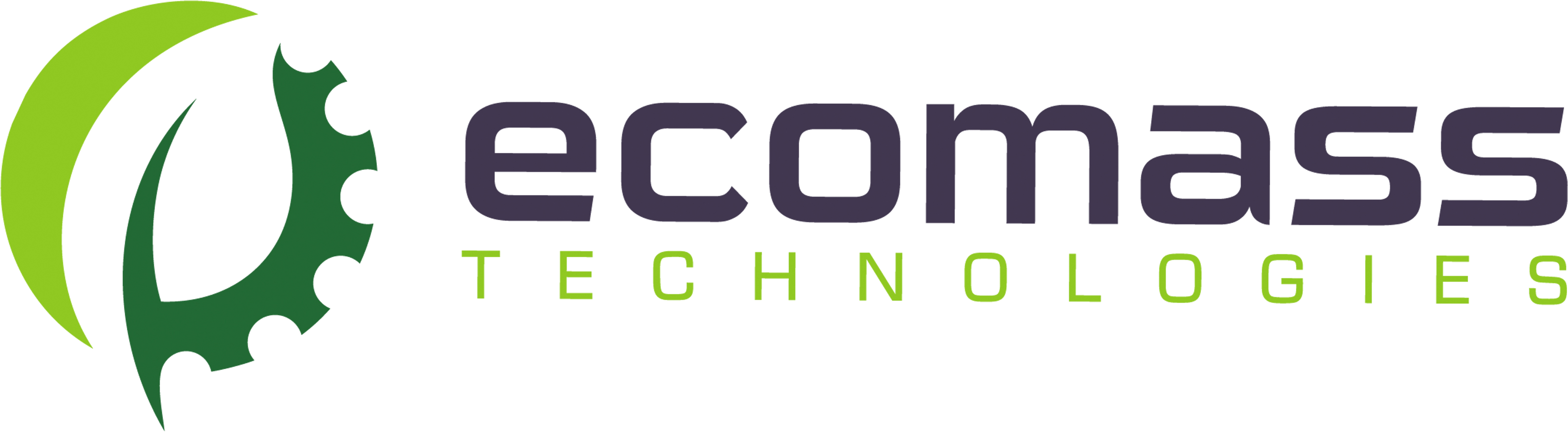
Standing tall at 24 feet long, 13 inch high and 8.7 feet wide, Manitowoc’s new carbon fiber composite stinger is an absolute beast. It mounts the same way as the commonly used steel version, but it truly packs a punch, for it offers the same 8600-lb maximum capacity while presenting a greater degree of flexibility, a more efficient design and a better lifting experience. Manitowoc unveiled the machine at the ConExpo-Con/Agg show in Vegas last month, and is expecting to offer the option in its Grove 700 Series TMS cranes and Grove TMS9000-2 cranes by the fourth quarter of this year.
Dr. Sammy Munuswamy, a senior principal engineer of the composite stinger project, says that the stinger “captures the power of light.” The modern-day world demands lighter and more efficient cranes that are able to get from one place to the other with ease, and that’s where high density materials come into the picture. According to Munuswamy, “the use of a carbon fiber stinger helps with both and we (Manitowoc) now offer a lighter crane component without compromising structural performance.”
The composite stinger is manufactured using composite materials which add stiffness and strength to the stinger, but still allows it to be 35% lighter than its steel counterpart. If combined with a synthetic fiber rope, the crane can be lightened dramatically. Weight has always been important for crane design, and it becomes even more essential for mobile units such as the taxi crane that are expected to transport themselves as self-contained units.
The ends of the composite stinger have the same steel components that are currently used in the existing steel version. “We wanted to retain proven sheaves and shafts of the steel stinger so that users will be able to leverage their existing mounting procedures,” says Munuswamy. The stinger also mounts the same way as the steel version. It swings out front and stows at the side of the lattice before pinning itself into a workable position. The mounting and stowing processes can easily be managed by a single operator.
The final Manitowoc prototype was tested for stability, function, structural integrity, resistance to deflection, stiffness and other key criteria. The Manitowoc team also put it through numerous cycles on a test bench to ensure that the strength and fatigue life met industry expectations. The end result is a stinger that is easier to handle, far more efficient, incredibly helpful when it comes to projection edges, lighter and stronger. The use of high density materials also allows the stinger to boast of a better reach, load capacity and tip height.
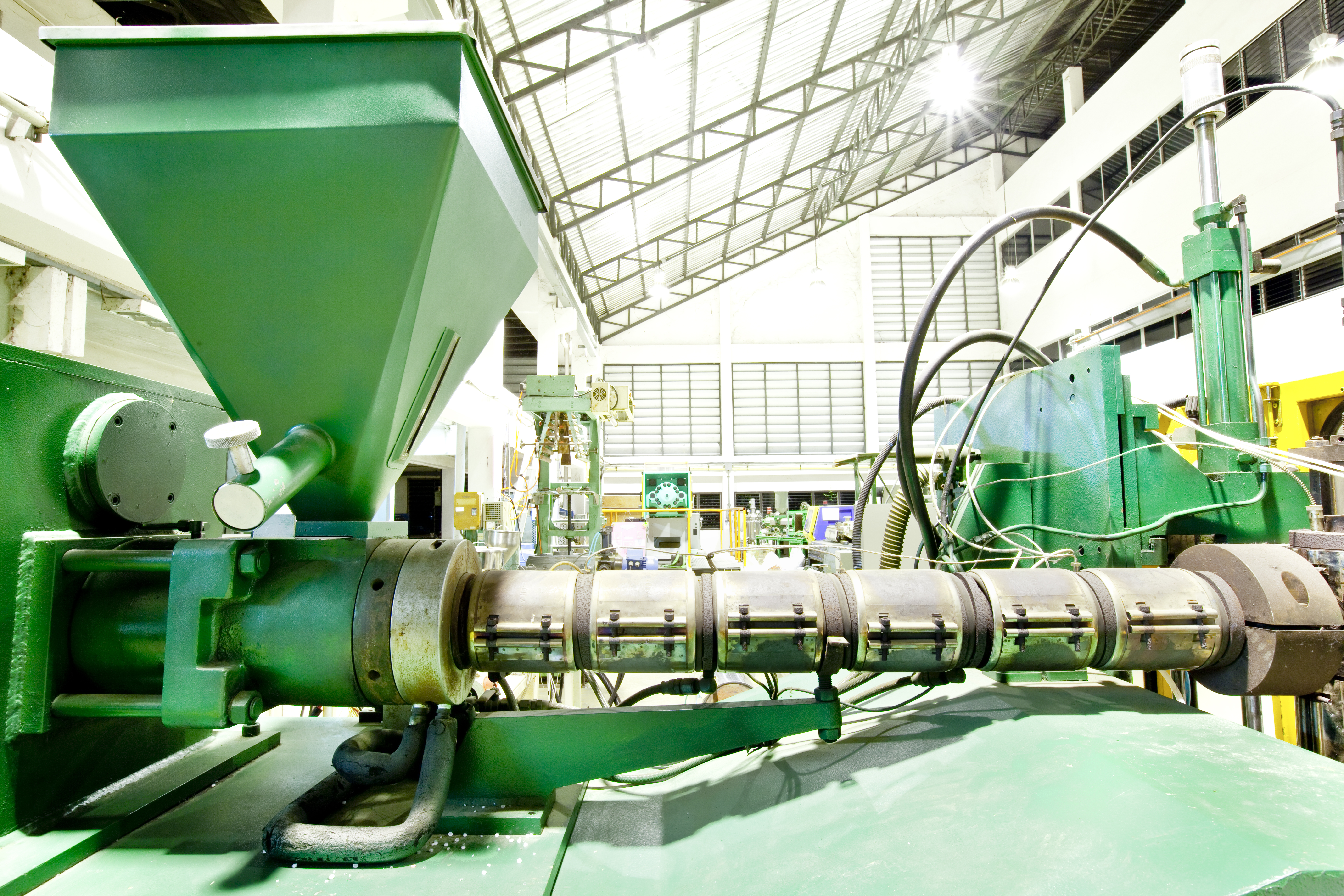
One of the biggest advantages of composite materials such as carbon fiber is that the fiber allows greater control over the amount of material, which means that it can be added wherever it is needed the most, thereby allowing the creation of a structure that is efficient and strong. In contrast, steel is used in standard plate sizes, which means that extra material is added. Other key features include vibration dampening materials to reduce noise and vibration and resistance to rust.
The global economy in the 21st century is driven by experiences and products that offer an emotional connect to the consumer are likely to dominate their respective markets. It’s no longer about being the longest, strongest or toughest. It’s about being the best while being the easiest and cheapest to work with.
0 comments:
Post a Comment